Advanced Space Propulsion CISAS Propulsion Group
The Hybrid rocket propulsion group carries out CFD simulations to support system design. CFD codes allow comparing different rocket configurations in terms of their efficiency (or of other specific parameters of interest) before testing them.
In this way, it becomes possible to select some specific designs among the others, reducing the overall test number and consequently the amount of money required for the system development.
CFD analysis is also important to acquire a greater insight into the physics of different phenomena, such as injection, flame stabilization, etc.
Our group mainly deals with:
-
injection problems and characterization, analyzing different injector types and with different oxidizers (both liquids and gases)
-
combustion investigation, considering different combustion chamber geometries, pre or post combustion chambers
-
devices to be used to enhance the system performance in terms of efficiency
-
studies for TVC (thrust vector control)
The hybrid propulsion group also develops 0-D and 1-D computer codes able to represent hybrid rockets physics.
In particular, a software was developed for the design, and another one for the analysis of the main instabilities which can be found in hybrid engines.
Simulations
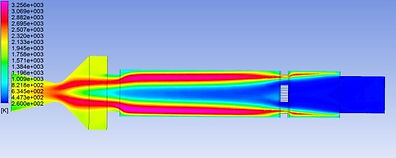




CFD analyses are always supported by adequate validation, performed by means of experimental data: experimental findings are compared with numerical results to assess the reliability of CFD prediction in terms of the different parameters being investigated. See below a qualitative example of results evaluation: the vortex flow patter as predicted by a CFD numerical code and as found onto a paraffin wax grain after fire tests.
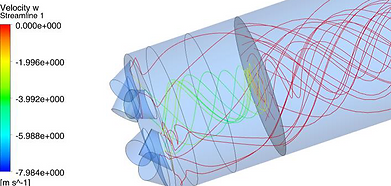

